Tour the Gauloises Yamaha pits - virtually!
Whilst the achievements of Valentino Rossi and Colin Edwards have helped propel Gauloises Yamaha to the top of the 2005 MotoGP teams' championship standings, their success would not be possible without the hard work of a dedicated crew of staff inside the pit box.
The first job for the pit crew at each GP, after they have parked the trailers on Wednesday morning, is to start unloading the materials, before intricately constructing the team's hi-tech home for the weekend.
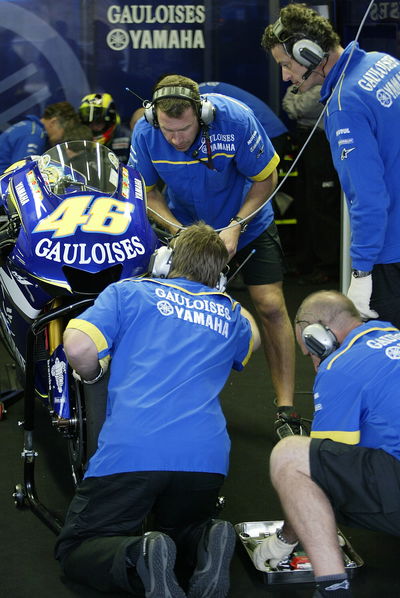
Whilst the achievements of Valentino Rossi and Colin Edwards have helped propel Gauloises Yamaha to the top of the 2005 MotoGP teams' championship standings, their success would not be possible without the hard work of a dedicated crew of staff inside the pit box.
The first job for the pit crew at each GP, after they have parked the trailers on Wednesday morning, is to start unloading the materials, before intricately constructing the team's hi-tech home for the weekend.
That takes until Wednesday lunchtime, when mechanics are then able to start working on the bikes in preparation for the race, following the instructions of their respective crew chiefs - Jeremy Burgess and Daniele Romagnoli.
Burgess and Romagnoli will have already met with their Japanese colleagues to find out what new parts are available for the weekend, make a plan for bike preparation and decide on the main changes to the gearbox and suspension settings from the last race.
Meanwhile, the data engineers use past information to try and predict potential problems the rider might have according to the demands of the circuit and prepare as many alternative solutions as they can.
The layout of the garage is designed to provide the team with readily available tools and the ideal surroundings to maximise their own performance throughout practice, qualifying and the race.
Witness how they are able to do this by taking a virtual tour inside the Gauloises Yamaha Team pit box, with comments from team director Davide Brivio, Rossi's crew chief Jeremy Burgess, team co-ordinator Marc Canela and the riders themselves (the numbers below correspond with those in the top two pictures - click to enlarge)...
1. Wall panels.
Davide Brivio: "These are made from ultra-light fibreglass. They are designed not only to look good but also to reduce the collective weight of the materials in the box. This is a major consideration because it helps us to reduce transport costs for the overseas races."
Marc Canela: "The panels are custom-made by a specialised firm near the team's base in Italy. Once packed into the transportation box they have an overall weight of 450kg."
2. Touch screen weather station.
Jeremy Burgess: "This is a small but important part of the garage. The Oregon weather station informs the engineers of the temperature inside and outside the box, wind speed and direction, air pressure levels every two hours for the last twelve hours and the current barometric pressure. It uses all this information to calculate the percentage of the likelihood of rain and gives us a live weather forecast throughout the Grand Prix weekend."
3. #46.
Davide Brivio: "This is now one of the most famous numbers in the world and it has a very special meaning to anybody involved in our sport. At the beginning it was very strange, a big emotion, to see the number 46 on our bike. At one time I never thought it would be possible to see that number in this garage but I'm getting used to it now!"
Valentino Rossi: "I have always been number 46 because it was the number of my father, Graziano, when he was a Grand Prix racer. In 2001 I had my first chance to change it to number 1 after winning the 500 title but I wanted to keep my own number - like Barry Sheene did with number 7 and Kevin Schwantz with the 34. Now everybody knows me as number 46!"
4. #5.
Davide Brivio: "The number five, of course, is for Colin Edwards. Colin has been a very valuable addition to this box since we signed him during the winter, because he is a very mature rider with a lot of experience. He is a very sensitive rider and he gives a very good contribution both to Michelin and to Yamaha, providing us with another valuable viewpoint. He is quite close to Valentino in terms of his requests for the bike setting and he has made a major contribution to the development of the YZR-M1."
Colin Edwards: "I was number 45 in World Superbikes in 1998 and finished fifth so in 1999 I used number 5 and finished second. I then ran number 2 in 2000 and won the title, so after using 45 and finishing fifth in MotoGP last season, I wanted to see if history would repeat itself!"
5. Tool drawers.
Jeremy Burgess: "The idea is to keep everything clean, tidy and readily available. These Beta tool drawers mean that there is never anything lying around and the mechanics can locate their tools quickly and efficiently, which is extremely important when they are working under pressure at a grand prix. One of the drawers is full of sweets... but I can't tell you which!"
6. Power supply.
Davide Brivio: "This is one of the most important things in the whole box! On Wednesday the first thing the truck drivers have to do, after parking up, is to connect the trailers to the power. Then the tyre guys make sure they have what they need for the tyre warmer stands. The circuit organiser provides the power so we don't have to pay."
Marc Canela: "As well as a total of 28 tyre warmers we also have twelve television screens within the box and four guest screens at the back that require constant power. The tyre warmers are the main drain on the electricity because of the heater elements, but even then they only use two amps each, and we rarely have more than ten warmers in use at a time.
"There are no heavy-duty tools in the garage and the only other drain is from the televisions and laptop computers. The circuit provide a maximum output of 100 amps for the pit box so we are well inside that - I would say we have similar power requirements to the average domestic household."
7. Air pump.
Jeremy Burgess: "This is just a standard air-pump, similar to the kind you use to fill your tyres at your local service station. The mechanics use it for all sorts of things but mainly to clear dirt and grit from the parts or blow water off the bike if it's raining."
8. Riders' tables.
Davide Brivio: "The riders always require a small table to hold their spare helmet, gloves and anything else they need. Sometimes they can be quite specific with their requests because they like to have everything in the right place when they want it. These tables are produced by the same company that provides the wall panels and they are made from fibreglass and aluminium."
9. Headphones.
Jeremy Burgess: "We use an eight-channel radio system which basically facilitates communication between pit wall and the box. It means that the engineers in the garage can prepare the necessary fuel and tyres according to any decisions we make during the session or the race. They also help to block out the sound of the bikes!"
10. Data engineer's shelf.
Davide Brivio: "In the past you will have seen Data Engineers standing over the bike with their laptops, downloading information directly from the bike. However, this specially designed desk is cut into the wall and is the ideal place for them to work from without getting in the way of the mechanics. It is fitted with a connection so that they can link up with the rest of the team network, or access the Internet directly.
"Communication is a very important part of modern racing and, along with the telephone lines at the back of the garage, this allows us to stay in constant contact with the engineers in Japan, who work throughout the weekend to help us overcome any problems we might face with the set-up of the bikes."
11. Back wall.
Davide Brivio: "This wall is slightly different to the others because it has a thin layer of aluminium mesh over blue Perspex. It allows the engineers working at the back of the garage to see through and keep an eye on events in the pit box at all times.
"In the back you can see the bigger main computer, where we analyse all the data together and get everything ready for our meeting after each practice session. The back section is also where the fuel and tyres are prepared and provides an area for our guests to watch the action.
"The oil is also stored behind this back wall. We go through at least 50 litres of Motul oil at each Grand Prix, although this can rise depending on engine usage. A well as bringing us the oil, Motul also bring us two litres of special hand soap for each Grand Prix so that the mechanics can clean the oil off their hands when they finish working!
"The fuel is worked out at approximately one litre per lap. For each rider we accommodate for 150 laps in a weekend, so that's a total of 300 litres per Grand Prix. This is raised to 500 litres for a test session, of which we have seven in total this year."
12. Carpet.
Marc Canela: "The carpet is made from a special non-flammable fabric, which is obviously designed to decrease the risk of a fire breaking out if there is a problem with one of the bikes. Like all the other materials in the box it is also lightweight and hard-wearing.
"The carpet measures 9x10 metres and comes from a special supplier near Barcelona in Spain. We use a fresh carpet at every Grand Prix, even the races outside Europe. For example this season I sent one carpet straight to Japan from Brno and then two more directly to Malaysia for the races at Sepang and Qatar."
13. Paper towels.
Marc Canela: "We go through around four rolls of paper towels at each Grand Prix, so 68 in total for the season, which are bought in Italy at the start of the year and stored at the team's workshop."
OFF SCREEN
14. Engine Starter.
Davide Brivio: "We have tried a variety of different starters since we first brought in the four-stroke MotoGP bikes. The current version is a heavy-duty electrical battery that uses a special kind of gel as opposed to regular battery acid, which is not allowed in the garage. It is built inside a lightweight aluminium frame, which supports the bike as special granite-coated rollers turn the rear wheel."
15. Overhead pulleys.
Jeremy Burgess: "One of these cables is the data link, which downloads information directly from the bike to the main computer at the back of the garage so that the engineers can have instant access. The other cable is a power source, which is used to charge the bike's main battery. This is only really necessary if lengthy data or electronic checks are taking place that would drain the power."
16. Rider & crew chief chairs (behind bikes).
Davide Brivio: "The relationship that takes place in this area is crucial. The Crew Chief is responsible for making decisions based on the rider's feedback so he has to be able to accurately discuss any problems he is having.
"Each rider has one Yamaha data engineer, one Ohlins suspension technician and a Michelin tyre technician. Valentino is particularly good at providing accurate indications to Jeremy. Their joint contribution has given Yamaha a lot of help in developing the YZR-M1."
17. Four-screen television frame.
Davide Brivio: "In the past it would take us a long time to set up each television individually but now we have four screens held in a custom-built box that needs just one power connection and one aerial feed. The frame is made at the workshop in Italy out of lightweight aluminium and uses the same fibreglass panelling as the walls."
18. Circuit name panel.
Davide Brivio: "This is new for 2005. The panel has the name of the grand prix written on it with the country's flag. At the end of the weekend we write the race results onto it and hang it up in the truck as a special memento."