Q&A: Charlie Dodd - SWRT's Logistics Supervisor.
Subaru's Charlie Dodd talks about his role as Parts Logistics Supervisor; how long he has been with SWRT; and a lot more:
Q:
Charlie Dodd - What does your job involve?
Charlie Dodd:
I look after the movement of all the rally car parts that the team is likely to need on each of the WRC events. I make sure that when we're on a rally, we've got the correct spares in our mobile workshops to keep the cars going. Basically it's my responsibility to ensure we've the right parts in the right place at the right time.
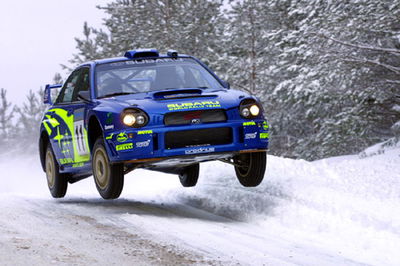
Subaru's Charlie Dodd talks about his role as Parts Logistics Supervisor; how long he has been with SWRT; and a lot more:
Q:
Charlie Dodd - What does your job involve?
Charlie Dodd:
I look after the movement of all the rally car parts that the team is likely to need on each of the WRC events. I make sure that when we're on a rally, we've got the correct spares in our mobile workshops to keep the cars going. Basically it's my responsibility to ensure we've the right parts in the right place at the right time.
Q:
How long have you been involved with the team?
CD:
Pretty much right from the start. I've been with Prodrive since we began working with Subaru 11 years ago. I started as a car builder, putting together the Subaru Legacies for drivers like Colin McRae and Ari Vatanen, then moved on to become a senior technician, then a number one technician and then workshop supervisor. I've been doing my current job for about a year now.
Q:
How do you make sure you never run out of parts?
CD:
To start with we have a standard spares package for each car, this contains most of the parts we'll need like windscreens, turbo-chargers, bumpers, spoilers and so on. But on top of that, we look at each event individually and work out which components are going to be used most heavily and which might need replacing. For instance on the tarmac rallies we'll take plenty of extra brake assemblies and front splitters. I've never run out of anything yet. Although It's been close on a couple of occasions...
Q:
What extra parts have you brought to Sweden?
CD:
The Swedish rally isn't an especially tough event for the mechanical components like suspension wishbones or brakes, but the bodywork can take a pounding and it's not unusual for back bumpers to be torn off by the snowbanks. On a normal event we'd take four spare bumpers for each car - that's two for the front and two for the rear - but in Sweden we've got five rears and three fronts per car.
Q:
Do you get involved in fitting the parts to the cars at service?
CD:
Sometimes if there's a lot of work to do I'll be drafted in to help out, but my primary role is to ensure that when the cars arrive at service the necessary components have been picked from the trucks and are laid out ready for the technicians to fit. I do still get involved in some fitting jobs, but they tend to back at our base in Banbury where we test-fit some of the larger, more complex assemblies like exhaust systems or turbo-chargers. We do this just to check that all the holes line-up and they slot into place easily.
Q:
What's it like working in the service area in freezing Sweden?
CD:
It's not too bad, we're all quite well insulated with fleeces, hats gloves and so on, and I'll certainly throw on as many layers underneath my uniform as possible. The technicians wear waterproof suits to keep the worst off, but although it sounds terrible to be under the cars in these conditions, you tend not to notice the cold when you're under pressure to get the car out on time. The worst thing I remember was that as parts of the cars are red-hot when they come in, the snow melts and drips on you if you're underneath. Believe me, at -10?c it's pretty uncomfortable when hot water trickles into your ear and then freezes again.