Q&A: Keith Murray (Subaru) - EXCLUSIVE.
by Rob Wilkins
Keith Murray is one of the men in the know when it comes to the logistical challenges that FIA World Rally Championship can throw up during the course of a season. As the transport manager at the Subaru World Rally Team, he knows just what it takes to get from 'A' to 'B' and then from 'B' to 'C' and then... ...'Y' to 'Z'.
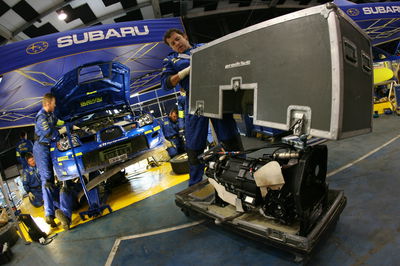
by Rob Wilkins
Keith Murray is one of the men in the know when it comes to the logistical challenges that FIA World Rally Championship can throw up during the course of a season. As the transport manager at the Subaru World Rally Team, he knows just what it takes to get from 'A' to 'B' and then from 'B' to 'C' and then... ...'Y' to 'Z'.
We caught up with him in September and here he speaks exclusively to Rallycourse and Crash.net Radio about the trials and tribulations of getting around the globe during the year, when the WRC visits 16 different countries and five continents...
Q:
Keith, just how big a challenge is the FIA World Rally Championship for the teams in terms of logistics?
Keith Murray:
It is huge. We have got 30 or 40 people to shift around - five or six trucks by road and we have also got air and sea for the long haul events. It is unique in some respects, in as much as we have to get there, which puts a bit of pressure on us.
Cost is a secondary thing because we haven't got any choice, as we need to get there and we need to get there on the date that the event starts, which is what makes it challenging.
2006 was a bit different as well, with the pairing of events - that adds another dimension, because we have got to do re-builds' in the field and that adds to the nightmare.
Q:
Roughly speaking how many miles or kilometres do the teams clock up during a year?
KM:
For road transport it is not as much as you think. For example we do Monte Carlo and Sweden historically as 'one event'. We go from here with the majority of the fleet down to Monte Carlo, which is probably 800-1000 miles and then we park up for the week. Then the majority of the fleet drives up to Sweden. We usually bring one or two trucks back here with the cars in and then we swap over. The other big thing is the wheels - we obviously have to swap them. So in terms of mileage, with the actual trucks you are looking at around 16,000 miles a year in total.
Miles covered by the team in total would be phenomenal once you include places like New Zealand and Australia. I wouldn't want to guess at that.
Q:
I assume the long-haul events in Japan, New Zealand, Australia, Mexico and Argentina present the biggest test?
KM:
They are in some respects but in others they are actually easier. They are because it is remote and you have got sea freight, with customs and so on, although we don't have customs issues in Europe now. You have got the weather which obviously has an affect. But at the same time it tends to look after its self. We have what we have to a certain extent.
Whereas if you are only in Germany, the engineers think they have got that bit longer to make some changes and everything else. Whereas when we are getting ready for somewhere like Japan, where we charter an aircraft, all the teams club together, the cars go on a given date, it doesn't move, because that is when the plane goes.
In contrast when we came back from Japan we had a truck going off to Cyprus and we actually delayed the one with the cars by 10 or 12 hours and then we double-manned the truck down to catch the sea vessel. There were actually two guys in there driving, legally you can then drive non-stop for 20 hours, which actually gets us to where we need to be from Banbury. That is something we are using more and more - both for testing and for the rallies, just to optimise the amount of time they are in Banbury.
All-in-all they are each different, the long hauls are easy in some much as you have got what you have got and the dates are fixed and you can't mess around with it so much. Although you then get into hand-carry - we have been known to carry dampers on aircraft, we have been known to take gearboxes before, but those days are numbered now I think with the increases in security [post 9/11].
Q:
I was going to say Rally GB would be the easiest in terms of logistics, but from what you have just said, I guess that isn't the case?
KM:
A lot of the guys actually regard it as being the worst event, because we don't actually go and set-up a base. If we go to Germany we set off generally so we are there on the Monday and we start setting the service area up and everything goes at the same time, because we need all the trucks there to get things sorted. Whereas with Rally GB we are always trying to leave things - it is staggered. It is case of: 'Oh that can go later' or 'oh the cars can wait' and that sort of thing. Bits tend to leave here as late as possible. I have seen us go straight from here to shakedown before, which makes it harder as you have got people spread about and in different places. Also not having the truck there to set-up the service area delays that a little bit. So again, in some respects it is hard but we make it harder for ourselves.
What I have always maintained is for Wales, we should actually decamp from here and go to Swansea, as if it was a 'normal' event and actually book into a hotel on a Sunday night and be ready to start on a Monday morning down at the service park, which is what we do at every other event. But finances dictated otherwise, it doesn't make sense to go and book into a hotel when you can just pop down there in 3 or 4 hours.
Q:
How much kit is moved around and how is it done?
KM:
For European events, we have a mixture of trucks - two specialist trailers, which are valued at about ?250 thousand each and are custom built to our specification. One takes the rally cars and contains all the spare parts. The other one has an office at the front for the meetings - it has a driver de-briefing room, it has got a wardrobe with the drivers' kit and everything in it and in the back it has got the specialist kit; gearboxes, engines and there is a bench at one side so the guys can work on it.
From that extreme we have got a regular trailer, very basic and it carries the bulky stuff. It has got things like the water, which we carry in bulk for drinking. We have got all the heavy stuff in there - tables and chairs for the hospitality and the TV's and all that sort of thing. So that sits in a basic truck.
Then we have got a tyre truck, which carries all the wheels and tyres for both the recce and rally cars. So there is a mixture of stuff. We have five-six trucks.
We have also got a seven car transporter, which we use to shift our recce and management cars. Then we have got a catering truck, which belongs to a sub-contracter, but it travels with us. So all-in-all we have probably got 60-70 tonne of kit dragging round.
Q:
What's the typical timeframe for an average event, in terms of when everything has to leave the team's base to getting to the event and then getting everything set-up prior to the rally?
KM:
What we tend to do, is work on being there on the Sunday night. There are lots of different reasons for that. One is due to the regulations which govern road transport. We try and get it so that the drivers don't drive the week of the rally, because they would need a day off in that week, as you can only drive for six days and then you need the seventh day off. What we tend to do is we don't let them drive Monday to Sunday prior to a rally. So we get all the driving done up to the Sunday [before the rally week starts]. Sometimes because in France, Italy, Spain etc, you can't drive on a Sunday, you have to get there on a Saturday night and the guys have a Sunday off in preparation for the week to come.
We have also got to balance that against the 'working time directive' these days, which is another legal nightmare we get involved in.
Generally speaking though and it obviously depends how far away it is, but for Germany we set off on the Friday night, around tea-time. We stop the other side of the channel and then set-off for Germany - it is a days' drive from there, so they are there on the Saturday night. For Monte Carlo, they will leave a day earlier. So, we are probably looking at a 12-13 day period for most events, when you are just driving there and driving home.
Recently we did Germany, where you have got a couple of days to get there, you have got the event itself and then it is straight up to Finland. What we did there, we actually had to contract in some drivers. We had two spare guys back here who drove some trucks out there for us to help us out, but the rest were contracted and actually drove up on the Sunday. Obviously the guys who had been involved in the rally couldn't drive - they had run out of hours by the time Sunday had arrived. They flew up on Monday and joined the trucks up there. They arrived on the Tuesday and then set it all up again. So that trips was probably getting on for 20 days away.
Q:
As you say, Germany and Finland took place on back-to-back weekends this year. How big a strain was this?
KM:
It was a good idea, but what doesn't help was that they were obviously on different surfaces. For example, just a small part of the job is the recce cars, we have three recce cars and the recce cars had to leave Germany to get up to Finland. So, we had to send another three cars across to use as safety cars but as luck would have it we have changed our recce cars this year for a new model. However the wheels are different on both models - so we had to take wheels for the new model for the recce and wheels for the old cars for the safety cars. We also had to take the gravel wheels for when they got to Finland and it just kept adding up.
It was phenomenal the amount of stuff we were actually shifting and we didn't have that much spare space. We ended up, because we may have written-off an entry car in Germany, we had to then have a spare car ready in Banbury to go to Finland. But to get the car to Finland in time it actually had to leave Banbury before Germany had finished. In the end we had a van full of spares and kit, which we had used on the Friday and the Saturday in Germany and we had an hour pick-up with a covered trailer with a rally car in it, a complete car ready to go, and they set off Finland bound on the Saturday night. The idea was they would catch the ferry across to Sweden and they ended up in port first thing on Monday morning. The first thing they did when they got off the boat was to ring up and see if we finished Germany with two complete cars. In this case the answer was fortunately 'yes we did' and the guy with the rally car and the trailer just turned around and got back on the boat again. The guy in the van just carried on, on his own up to Finland and that was the re-stock for the Finland Rally.
We have got a very similar situation with Cyprus and Turkey. We are going to have to leave Banbury again, this time it is going to be with a rolling shell, of which will be in mid-France before the rally finishes and if we have two cars complete in Cyprus without too much damage, that vehicle will just come straight back again. But the van will carry on - again we have got a re-stock transit full of bits and pieces.
So the idea of back-to-backs is good in so much as you just roll on, but in the great scheme of things more gets added in. It is not just a straight saving, like everything else, you have to pay back somewhere with some of these things.
Q:
Talking of some of the potential problems or pitfalls, what are the other ones that Subaru have got to try and avoid?
KM:
Being late is the biggest thing we have to try and avoid, but to a certain extent once you are on the road you are definitely in your own hands. It is like, if you get a puncture and it holds you up for a couple of hours - but we try and build that in the schedule. Touch wood, we have never had anything more serious than that.
However once you get into sea freight there is so much that can go wrong. I remember a few years back we had sea freight heading to New Zealand and it was fairly tight in the schedule anyway, and it got into Kula Lumpur and for reasons that escape me now, the feeder vessel didn't pick up any containers in Kula Lumpur, I think it was full, so it just sailed on by. So our containers had been dropped off in port ready to catch this feeder vessel and they didn't make. We had a week in hand and the next feeder vessel came along three or four days later and it was full too so it didn't stop either. At that point in time we had to send somebody from Banbury to Kula Lumpur to go down to the docks, empty everything out of the containers. They then decided what was crucial to get to NZ and we stuck it in an aeroplane and we flew it from KL to Auckland. The rest of the stuff was popped back into a container and it actually got there on the last day of the rally. So in hindsight we did the right thing sending the guy down there but it is obviously not the cheapest way of doing the job. It is just what you have to do sometimes though to get the job done.
Airfreight is pretty straightforward, because generally the plane doesn't stop anywhere. We have had little issues. One of the problems now-a-days is the size of the planes - a 777, which is a pretty popular bit of kit now-a-days', you can't get a rally car into the cargo doors as easily as you could on a 747. The rally cars also only fit on certain parts of the cargo deck. So you have got to watch which aircraft are on the route. It is just something else you have got to be aware of really.
Q:
Going back to pairing events, Rally GB looks set to be paired with Rally Ireland, again like Germany and Finland, the two events are different, one is on gravel and one is on tarmac. Is this likely to be a problem too?
KM:
It will probably be a lot better for us than it will be for the French [Citroen] for instance, because obviously we are going to be coming back to GB, which should be quite easy to get sorted out really. We haven't looked at it in any great detail yet, but one of the thoughts I have got, if push comes to shove, we could actually come back into Wales with the trucks and just go straight there. We could always run stuff down from here in Banbury if we had to with the trucks just to top-up. At the moment providing the ferries works and the weather is OK, there shouldn't be too many dramas getting back from Ireland to Banbury and then popping down to Wales later on in the week. So that should be a lot easier.
It is just this remote thing, when you are in Germany, this year, I said we had sent that van with the spares in to Finland, we also sent another van to Germany on the Sunday with some other spares, just stuff that might be needed. That is a 24-hour trip for somebody in a van, whereas with GB at the end of the year, you are only 4 or 5 hours from Swansea, so it is not a big issue at all really. It doesn't look to be that much of a concern anyway.
Q:
When events are paired or take place back-to-back, I assume, from what you have said, that means you have to have more kit available?
KM:
Yeah, you need re-build kit - bumpers, doors, that sort of thing because no matter what you do, you want to get the car looking its best to start the event when it goes over the start ramp. It is insurance, like everything else you have to take more than you will hope you will need - but sometimes if you have a bad day it all gets used.
Likewise going back to Germany and Finland, when Petter [Solberg] had his accident in Germany [in the shakedown on the Thursday], we used quite a lot of stuff before the rally had started. That adds another dimension to the thing. It will be interesting to see what happens in 2007, because we go from Finland to Germany on the calendar. At least in 2006, when we went from Germany to Finland the cars were in quite good nick having been on tarmac. Whereas in '07 we have to go to a gravel event before we go to tarmac and that will be a far harder rebuild when you get down to Germany. We will have to see though it will depend on how the ferries run.
That was another problem this year, we were promised a boat and in the end they actually put on a boat that was quicker than they thought they would have, because they had built a new boat and put it straight into service. There are all things like that that help the job along.
I think something that is proposed to change is that France and Spain may swap around and then you have got the added difficulty of being in Corsica and not many ferries come off of there. Also when they moved the base of Spain, a year or so ago, that extra bit of distance, made quite a difference to us. Whereas before you could do it in one hit if you like off the ferry, but as soon as they added in moving the event to Catalunya, we had to get extra drivers' in. So there are little things that get added in that seem to be of no real significance until you starting looking into it in detail - and it is like: 'Oh hang on - that has made quite a bit of difference actually'.
Q:
Historically speaking, how has the logistical challenge changed over the years? Has it got harder with more events being added in and now going further a field, like when Japan and Mexico joined the fold in 2004?
KM:
It has changed so much - but as much as anything we have forced a lot of changes on ourselves. I think all the teams have been cutting their cloth accordingly for a few years now and I think we have always been pretty smart, or I like to think we have, in how we did it.
Years ago back in 1994 and 1995 we had the Asia Pacific Championship, as well as the WRC to do, where we would be running in Thailand, Malaysia and Indonesia, before some of those events came into the WRC.
As for Japan, I have gone to every Japan rally we have done and it was my fifth one this year, because they ran a tarmac event for a couple of years in the hope of getting into the championship and we went along with Toshi [Arai]. It is like a lot of these things the more familiar you get with routines and what not, the easier it gets.
We put pressure on ourselves as well though, because we are always trying to better it the next year. It is very seldom we go back somewhere in exactly the same way as we did the year before. There is always something you can leave off or something extra you can take or you can shave a day off the time or whatever.
I think that the biggest change now-a-days is - maybe 5-6 years ago we did an awful lot more sea freight because we thought it was cheaper. But then you had to have more kit, because you needed two sets of kit. Where as now, although we have still got a second set, it is a vastly reduced amount of kit to what we use to have. In Japan we had two forty foot containers and two twenty foot containers on the sea freight, where as I can remember the days of having ten containers sitting with kit in them, because we took management cars, we took mini-buses, we took three or four vans. Now with the centralised servicing we take one truck with us, just in case we have to do a remote-shakedown.
It is little things like that where the organisers can help us. Remote-shakedowns are just a nightmare - you have to have a vehicle to get your kit up the road. It happened in Cyprus, it means we lost a vehicle out of the service area which means we can't then put the awing on the side of it and get everything set-up until the truck comes back after the shakedown. Little things like that can make a big difference to us.
Q:
How long have you been transport manager then Keith?
KM:
I have been transport manager three or four years. I have been here at Prodrive since 1988 though, so I am actually in my 18th year now. I spent the first three or four years working on the workshop floor with the cars and then certainly since the start of the Subaru WRT, I was involved in the parts to start with and then that just moved on into the shipping thereof, and then the vehicles came under my wing too. I have been doing it a while now it must be said. I think the first time I started was 1992 or something like that. I have moved on a bit now. I get to go to one or two events a year and I have got a very good guy under me who runs all the freight now.
Q:
There will be three new events in 2007 - in Norway, Ireland and Portugal, does that add a new challenge I assume?
KM:
Norway will add a new challenge, as it is not in the EU. So I think the organisers are going to try and sort something out so we have a bond that goes in there. So we don't have to do too much paperwork. But other than that it shouldn't be too big a problem, because obviously we are in Sweden anyway and the fact Petter comes from Norway should help us hopefully. They are so enthusiastic too - they want the rally to be there. That makes a big difference.
Portugal that will be OK - we have been there many, many years ago. I can remember going to Portugal when it was tarmac to start with and then you moved onto gravel after a couple of days and it was a sort of five-day event. I can't see that being a big drama.
Ireland could surprise us yet, because they ran it this year and got the approval to run it in the championship but whether they are aware how big these trucks are now I don't know. It all depends' what the service area is like. We have got some big kit that we need to get in there and it is big kit you don't want to scratch. It will be interesting to see how they can handle that side of it.
Q:
Finally, can you give us any figures on how many people are needed at each event and what it costs for a 'typical' event, if there is such a thing?
KM:
Probably looking at about 30 - it is not something I know off the top of my head. From our side, four truck drivers' go and a parts man. Whereas the actual team, will be restricted to five guys per car in 2007 - this year we are on six. Then there are all the add-ons though, we have catering staff, generally four or five of them, there is the marketing people and the weather people and so on. I think we would be looking at 30-35, whereas a few years ago we would take sixty people.
That is something else that has changed, just the size of the team. It is a lot less than in the 'good-old-days' when we had ten vans, a couple of helicopters and some safety cars to get in the country.
As for a cost for an event, that is very difficult to say, because it changes. Now with EasyJet and RyanAir they have played a part in what we do as well. You have got extremes of tickets this year for New Zealand, which cost something like ?720-?750 plus the tax. Whereas we can go to a test in Sicily and the tickets are ?8 plus tax. I don't know if I can put a value on that.
Q:
Can you give us percentage of Subaru's or a teams' budget roughly that goes on logistics?
KM:
On the actual air and sea freight side I would expect to have to spend in excess of ?750 thousand a year moving stuff around. Then if you add in the flights on top of that, I wouldn't be surprised if we spend half a million pounds on flights now-a-days. So it is quite a big spend.
As I say though the way we go about it, so much has changed. We use to have a travel office here on site, where we had two people, who were employed by a travel agent and they just sorted all of our travel out. Now as things have evolved and you can book online, they have actually gone now. The woman that does all our hotels and flight bookings etc, a lot of the events, she is booking the flights herself, generally where EasyJet and RyanAir go. Then we use a travel company for the long haul events but I would think now-a-days, 50 per cent of the events we go to, we book the flights ourselves.
Q:
Thanks for your time Keith.